
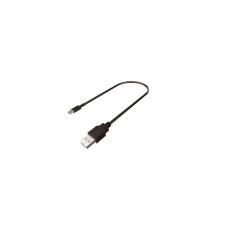
When the servo experiences a brown-out/under-voltage event and reboots, it will briefly enter its bootloader mode and listen for special commands at a fixed baudrate to update its firmware. 1/5th is not guaranteed to not eventually cause an over-temperature shutdown, but it should be some time before the shutdown occurs. If the servo is stuffed in an insulating structure, then it will retain more heat. If the loading is greater than that, then it will produce more heat. The usable/working torque of dynamixel servos is ~1/5 of the stall torque. If you do not use forced cooling, then you have to completely turn off power to the servos/buss and wait for the internals of the servo to cool off on their own.

When a servo overheats, simply leaving the torque disabled will not be enough to clear the over-temperature fault unless you force cool it (fans, CO2 dusters, etc.). To prevent damage to the motor and electronics, the controller within the servo will cut power to the motor if it experiences an over-temperature condition (also if there is an overload condition). The process of producing torque generates heat in the servo's motor, and if the heat is generated faster than it escapes the servo then the motor can become dangerously hot. How long can you hold it there? The servos are the same way. Pick up a heavy book or weight and hold it straight out from your body level with your shoulders. Contact Reseller/Robotis for RMA motor replacement rarely/never covered under warranty. Remove from service immediately to prevent further damage to the servo and/or damage to other servos on buss.Likely a borked motor (damaged brushes and/or shorted commutator).Does it show up on the dynamixel buss at all?.Did you check for damaged wires and/or loose connectors?.Likely a gouged or broken tooth on one of the gears.Does the servo click/crunch when moving?.Can the joint/servo be moved/rotated by hand when not powered?.Contact Reseller/Robotis for RMA PCB replacement should be covered under warranty. If not found by RoboPlus Dynamixel Manager during an exhaustive search when connected and powered alone, then it is probable that the communications ICs of the servo's control board have been damaged.Does it show up on the dynamixel buss (alone or with others)?.Check if it is found by RoboPlus Dynamixel Manager when connected alone to a properly configured USB2Dynamixel and power supply.Does the servo flash its LED when first powered on?.The servo may have had its ID reset to '1' during a low voltage reset.Sometimes older cables can develop intermittent shorts, and sometimes connectors need to be reseated a few times to ensure a good electrical connection.Cables can easily snag on frames and/or get torn/sliced apart if not well routed.Cable protection wraps can sometimes pull connectors out of servos.Probably a damaged wire or loose connector.Do any servos suddenly stop responding and/or go limp, but not the entire bot?.Is the power supply adequate (12V/5A minimum)?.How old is the battery (how badly abused)?.AX have re-usable bushings RX/EX/MX have replaceable ball bearings). If so, you will need to order a replacement gear/bearing kit, but may be able to replace only the large output gear and its bearings (if any. You may have sheared off the output spline.
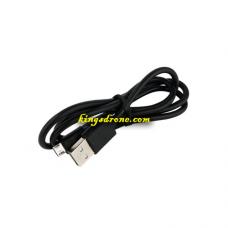
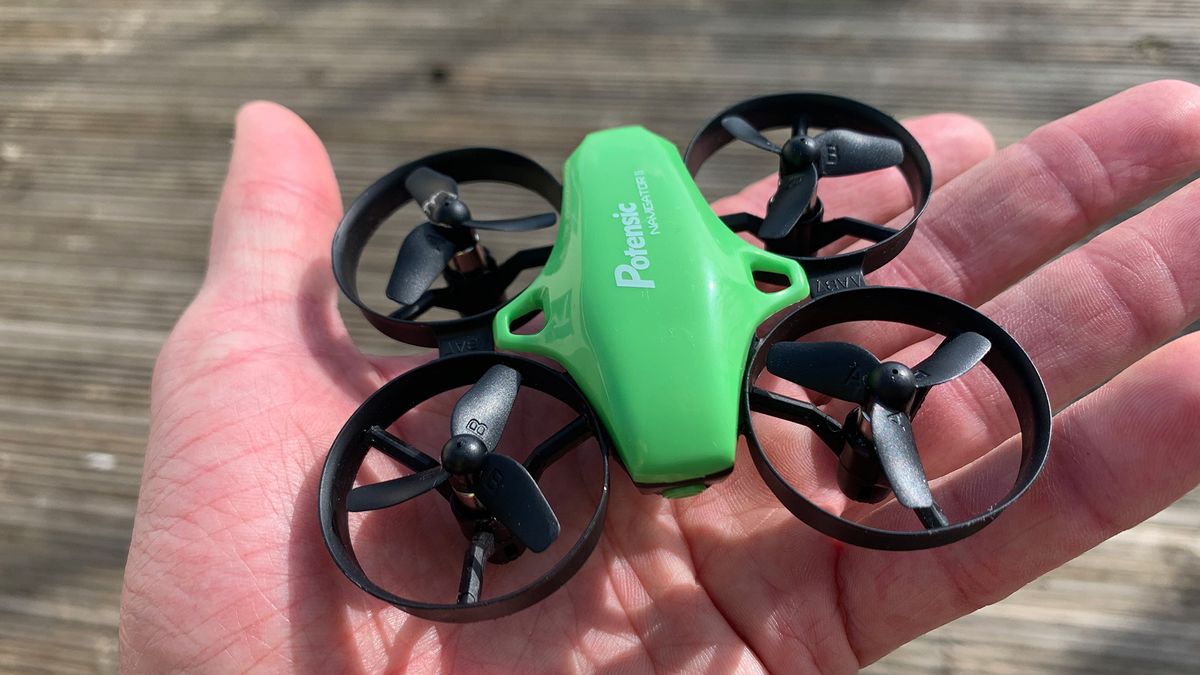
Does the servo horn rotate by hand when it should not (especially in one direction)?.If the horn never moves, or briefly moves only after a 'kick-start', before throwing an overload error then the motor may have been damaged. You may be driving the servo to self-interference or the frames may have snagged on something (e.g. Overload error is caused by exceeding the internal time limit where the servo's microcontroller will attempt to continue driving the motor even though the horn is not moving to its goal position.Over-temperature error is usually caused by pushing the servo too hard and/or too long.May be 'over-temperature' or 'overload' error.From 'Diagnosing a DARwIn-OP' for UGA Theatre students and ' RX-64 shutting down.'
